While solid plates and sheets of titanium form the protective skins and structural backbones of modern technology, it is the hollow form—the titanium tube—that serves as its circulatory system. These remarkable components are essential for transporting critical fluids in the world's most demanding environments and for providing incredible structural strength where weight is a primary concern.
From the complex network of hydraulic lines in a jet aircraft to the heat exchangers in a coastal power plant, titanium tubing is a high-performance solution chosen when reliability is non-negotiable.
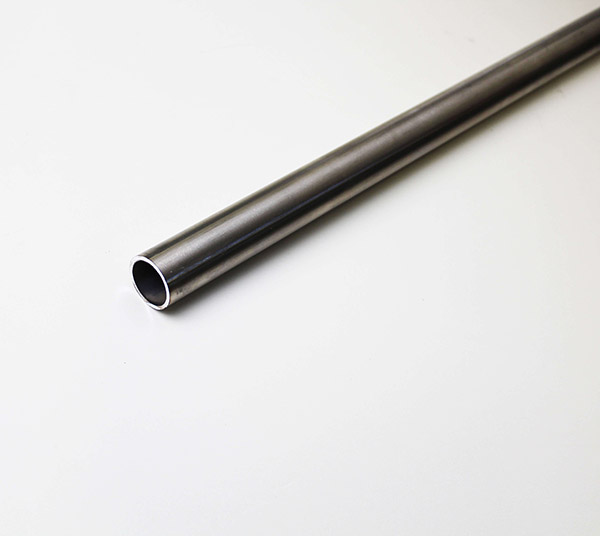
Defining the Form: Tube vs. Pipe
In engineering, the terms "tube" and "pipe" are not interchangeable. The distinction is crucial:
- Tube: A tube is generally defined by its precise outside diameter (OD) and a specific wall thickness. Tubes are used in applications that require precision and structural integrity, such as in aerospace frames, hydraulic systems, and heat exchangers.
- Pipe: A pipe is typically defined by a nominal inside diameter (ID). Its primary purpose is to transport fluids or gasses from one point to another, as seen in plumbing and large-scale industrial processing.
This article focuses on titanium tubes, which are prized for their exact dimensions and superior material properties.
Manufacturing Methods: Seamless vs. Welded
Titanium tubes are typically produced in two primary ways, each with distinct advantages:
- Seamless Tubes: These are created by piercing or extruding a solid round billet of titanium to form a hollow tube. Because they have no seam or weld joint, they possess a uniform structure, superior strength, and higher pressure ratings. This makes them ideal for critical high-pressure applications.
- Welded Tubes: These are fabricated by taking a flat strip of titanium sheet, rolling it into a tube shape, and then welding the seam together. Welded tubes often have more consistent wall thickness and can be more cost-effective to produce. Modern welding techniques make them extremely reliable for a vast range of applications.
Why Choose Titanium Tubing? The Core Properties
The demand for titanium tubing stems from its unparalleled combination of material characteristics.
- ????️ Exceptional Corrosion Resistance: This is arguably the most important property for titanium tubing. The metal's natural, self-healing oxide layer makes it virtually immune to corrosion from seawater, chlorine, industrial chemicals, and other aggressive media. This is why it is the material of choice for desalination plants and chemical processing.
- ???? Superior Strength-to-Weight Ratio: Titanium tubes provide the strength of steel at roughly half the weight. This allows engineers to design systems that are both robust and lightweight, a critical factor in aerospace for hydraulic lines and in high-performance sporting goods like bicycle frames.
- ???? Excellent Heat Transfer Efficiency: In heat exchangers, titanium's stability allows for the use of tubes with thinner walls compared to other metals. Thinner walls, combined with titanium's resistance to fouling (the build-up of deposits), result in highly efficient heat transfer, improving the overall performance of the system.
- ???? Biocompatibility: Like other forms of titanium, the tubing is non-toxic and not rejected by the human body. This makes it suitable for creating surgical instruments and components for medical devices.
Key Applications Across Industries
You will find titanium tubing performing critical functions in a variety of high-stakes environments:
- Heat Exchangers: This is a primary application. Titanium tubes are used in condensers and heat exchangers in power generation plants, chemical processing facilities, and offshore oil rigs where they are constantly exposed to corrosive fluids.
- Aerospace: Essential for high-pressure hydraulic lines that control flight surfaces, as well as for structural components in the airframe where strength and low weight are paramount.
- Automotive: Used in high-end, performance exhaust systems where it reduces weight and can withstand extreme temperatures.
- Medical: Fabricated into surgical instruments, cannulas, and other devices that require both strength and biocompatibility.
- Sporting Goods: The frame of a high-end racing bicycle or the shaft of a premium golf club often utilizes titanium tubing to provide professional-grade performance.
Conclusion
Titanium tubing is a testament to advanced material science, offering a solution where other materials would quickly fail. Its ability to transport fluids reliably in highly corrosive environments and provide lightweight structural support makes it a cornerstone of modern industry. Whether it's helping to generate clean energy, enabling safer air travel, or enhancing a medical procedure, the humble titanium tube is a hollow pillar supporting technological progress. Visit https://www.chinatitaniums.com/ for more information